Firstly, float levels were too high at 12mm. This tended to cause overflow. Resetting to 15mm gave a lower than expected fuel level (consistently around 30-32mm) but has stopped the overflow.
Secondly, the acceleration pump on the rear carb was set for a larger pumped volume than that on the front- and probably rather larger than required. Resetting this has reduced excess fuel supplied during starting.
Thirdly, a poorly adjusted carburettor linkage had led to misfiring/not firing in cylinders 1 and 2
And - superimposed on all of this was a damaged AB14-to-pickup connection lead resulting in sporadic loss of spark which hopefully I have also now fixed by fitting a new WM12 connector and lead. I can replace this pickup entirely and new ones are available from H&H Ignition services at £40.
If we assume that I have at last sorted these problems then its time to optimise the carburation ... so, finally, I can move on! I did want to do this job properly- in the end I don't think I did, but here at least is my research and the reasoning behind my adjustments. Please feel free to comment (and dare I say help!).
Setting up the carbs involves adjusting and equalising the amount of air drawn in through each barrel due to the induced vacuum of the motor, synchronising the movements of the butterflies in each carb so that this vacuum/air intake will alter equally in each barrel as the throttle opens, and adjusting the air/fuel mixture at idle. Only the idle mixture is adjustable, the mix at higher throttle openings is governed by the various jet sizes installed. After adjustment the carburettor should give a smooth idle and this is re-set close to 600 rpm to complete the process
To achieve all this a DHLA45 carb has 4 adjustments that can be altered:
- The idle mixture control screw (1 per barrel, 4 in total). Sets the idle combustion mixture individually for each barrel. May be covered by plastic tamper proof caps.
- The air (or sometimes "idle") bypass screw which allows the 2 barrels in one carb to be balanced one to the other (1 per barrel, 4 in total). Maybe covered in metal tamper proof caps
- The throttle synchronisation mechanism- 1 adjustment screw that controls the the opening of the front carb relative to the rear carb and allows one carb to be balanced against the other.
- The idle speed screw- affects the throttle lever rest position for both carbs and thus the motor's idling speed (one screw)
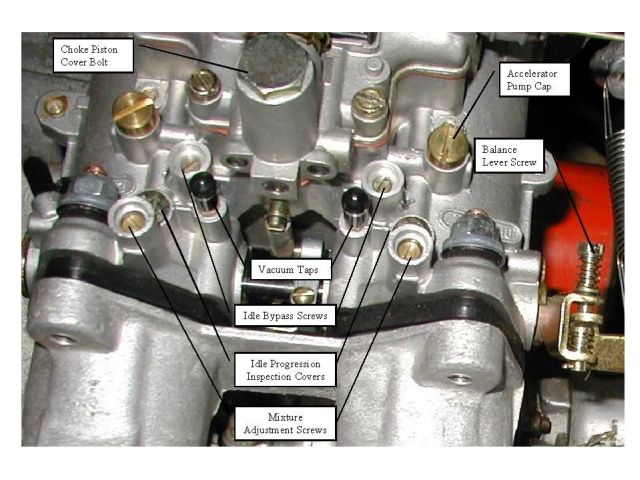
- Method from Lotusexcel.net
- Method for the Lotus Esprit
- Method for the Laverda* but note that if using this reference fig 4 is incorrectly linked in the original and doesn't display. You will find that figure here.
- Method for the Clan "Richards place"
- Method from Des Hammill's Book
- In addition I have found a specific description of the use of the Carbtune II for this carb in the Jensen Healey.
In the first approach, the idle control screws start off closed so that the weaker barrel can be identified. The idle bypass screw on the stronger barrel is then opened to admit more air and so reduce vacuum to match its weaker companion. When fully adjusted only one idle screw will be open in each carb- the second will be closed and that barrel effectively functions as a carb without such an adjustment.
In the second method all idle bypass screws are open at the start of the process and progressively adjusted (opened?) until balance is achieved. At this point all idle bypass screws will be open to some extent and so in every barrel there will be air coming past the butterfly and through the bypass system. Since some air comes through the bypass, this means that at any set idle speed the butterflies will be closed more than is achieved by the first method. This approach is more complicated but is said to give better control over emissions.
Both methods require that the butterflies in both carburettors move in synchrony as the throttle is pressed. This means ensuring that they are in the same position at at least one point in their movement. This match position can be set either functionally using vacuum equalisation (when closed); or physically as they move by checking that they pass a fixed point (such as one of the progression holes) together. If the spindles and butterflies are in good condition then it will make little if any difference where/how you set this match, but if the spindles are bent or the butterflies worn it may well do so. In this case setting for balance at throttles open may be preferable for smooth driving at the expense of smooth idle.
Similarly both methods require optimising combustion and thus reducing emissions. Emissions are measured either directly using a CO monitor, or indirectly with a colortune or by monitoring vacuum in that carb. Given that there are 4 mixture screws and the only domestic exhaust gas analyser is the Gunsons Gastester which I have found to be wildly insensitive even when used on single carb cars, I suspect this isn't practical. In fact I found the other two methods relatively ineffective as well (see on) and this remains the most significant problem I found in balancing.
My Approach:
Dellorto dont want me fiddling with these settings or they wouldn't cover them all with anti-tamper plugs! 'For once there is no sign of the bodging hands of the LBPO, so I would be only too happy to leave them alone but the car has had a chequered history and channels may be clogged or blocked. All the same I didn't want to risk upsetting what could be a perfectly adequate setting, so I wanted to check whether the preset adjustments were still applicable. I think that if they are correct, then it follows that balance will already be set within each carb. In other words both barrels should already be matched when idle mixture screws are adjusted to give maximum vacuum; effectively setting the idles for max vac should show the barrels of each carb to be matched and all I will need to do is adjust the carb linkage to equalise vacuums between them- and maybe check with the colortune that I'm getting good combustion. If the barrels do not match then the air/idle bypass setting may no longer be appropriate and I will need to start from the beginning.
Dellorto dont want me fiddling with these settings or they wouldn't cover them all with anti-tamper plugs! 'For once there is no sign of the bodging hands of the LBPO, so I would be only too happy to leave them alone but the car has had a chequered history and channels may be clogged or blocked. All the same I didn't want to risk upsetting what could be a perfectly adequate setting, so I wanted to check whether the preset adjustments were still applicable. I think that if they are correct, then it follows that balance will already be set within each carb. In other words both barrels should already be matched when idle mixture screws are adjusted to give maximum vacuum; effectively setting the idles for max vac should show the barrels of each carb to be matched and all I will need to do is adjust the carb linkage to equalise vacuums between them- and maybe check with the colortune that I'm getting good combustion. If the barrels do not match then the air/idle bypass setting may no longer be appropriate and I will need to start from the beginning.
It was simple enough to warm up the motor and connect the Carbtune spigots in place of the vac blanking screws and connect up the unit.
![]() |
Vacuum blanking screws replaced with plastic carbtune spigots... |
![]() |
... in both carbs. |
The pulsing effect was v bad until I realized I was holding the unit upside down (Duhhh !) and matters improved after that! The rear carb barrels were quite similar, but the barrels in the front were out both with each other and the rear carb.
Here was my first surprise.... all the methods I have read speak of optimising the vacuum using the idle mixture screws as the first step, and readjusting them with this screw throughout. I was shocked therefore to find that in my hands the idle mixture screws had virtually no effect on vacuum at all! I tried a colortune but they had little effect on that either. Screwing them all the way in did lead to a misfire and a stall but there was practically no effect until the motor became non-runnable. I did find that the rearmost idle mix screw seemed to leak and gave a steady reading only if pressed down. I took that one out and found it lacked a spring completely.
![]() |
Look Ma- no spring! Even though... |
![]() |
... springs were present in all other idle mix screw holes |
All the screws were a bit scratched and the "O" rings looked worn although I doubt any were actually unserviceable. Nevertheless this might be part of the explanation?
In any event I decided to change all the screws,"O" rings and washers, and of course to fit a new spring in barrel 1.
New idle mix screw left- old one right |
In any event I decided to change all the screws,"O" rings and washers, and of course to fit a new spring in barrel 1.
Nice new bits from Eurocarb |
Since the carbs didn't seem to be balanced, I would have to deal with the idle (or air) bypass screws, so I removed their anti-tamper plugs (drill through and lever off) and tested their settings. The rearmost bypass screw on each carb was fully closed so it appears my carbs have been balanced previously by the former one-air-screw-shut approach. The second screw was positioned at 3/4 turn (rear carb) and 1/4 turn (front carb). For completeness I replaced the O rings on all 4 of these screws as well and cleaned out the bypass passages with carb cleaning spray. All the screws looked fine apart from the forward screw in carb one which seemed to have suffered some form of combustion effect. The screw was darkly discoloured and pitted and I may need to replace it eventually in the meantime I swapped it with one of those which had been fully closed.
I reassembled the carb and ran the motor up to temperature again to start the balancing process. However, having made these changes there was still no obvious difference in idle mixture screw response and the idle screws still had little effect. This is new to me: I am used to adjusting simpler motorcycle carburettors and in that case the idle mixture screw certainly affects combustion, so before I went on any further, I tried to get my head around it. This is what I now think-
Air bypass screw from front carb- seems to have been burned. |
My two-penneth...
The difference between these DHLAs and simpler carbs are many- but one obvious glaring difference is the presence of progression holes. These are meant to be "progressively" exposed at low speeds as the throttle opens, they supply extra fuel and avoid over leaness at low throttle. All the balancing methods I have read assume that all progression holes will be closed when the motor is at idle... or as they put it the butterfly will be "manifold side" of the holes. However, in my case they were not! Having checked with the forum others find a similar thing too. Even when the idle speed screw is backed off completely, and thus the throttle fully closed, the throttle butterflies return to a position across the first progression hole. Ok this may possibly be closing it off, but the motor wont run like this and only a few turns on the idle speed screw would open the first hole. This is seen clearly using my endoscope to peer up through the progression holes (cap removed) from inside the carb.
The working of the progression holes and idle screw is shown below in a diagram taken from the Laverda owners club. For idling- fuel is drawn up through the idle jet (20), mixed with air coming from the channel (19) in the emulsion tube and fed out to the idle mixture screw outlet (22). On the way this mixture passes the progression holes under the plug (23), and provided these are all closed by the butterfly(13), or missing entirely as in a simple carb, then all of the mixture is drawn out past the idle mixture screw by the vacuum in the manifold. Its important to note that the idle mixture screw- despite its name, doesn't control the composition of the fuel/air mix passing by it, but in this simple case it will control the quantity of this fuel/air mix that flows past it. Opening the screw will allow more fuel/air mix in to combine with throttle-metered air entering from the front of the carb through the Venturi, so at any given throttle setting the idle mix screw can regulate the amount of fuel in this final combustion mixture.
But... what happens if as in my case one of the progression holes is uncovered? Now the idle mixture can exit to the motor through two routes: past the idle screw as before but also through the open progression hole. Its important to note that its the same mixture being drawn though both exits by the vacuum inside the carb. Adjusting the idle mixture screw can regulate the amount of fuel/air mix that passes by the screw just as before, but as the screw shuts, more mixture will simply be drawn in through the progression hole and the total amount admitted will not necessarily be changed (see small inset diagram above). In practice there may well be some effect on the total drawn in since the vacuum in the carb will have different strengths at the prog hole compared with that at the idle screw, but this is subtle compared with the situation in a carb lacking prog holes and may explain why I found that the idle mixture screw was essentially functionless.
If what I have said above is correct then it follows that the idle mix screw will be most effective when the throttles are as closed as possible- perhaps completely closed. This would mean that the idle speed screw is set almost out and the air required to allow the motor to idle will need to come in part - possibly a large part, through the idle (air) bypass system. In other words the second adjustment method would seem to be preferable. This would give a responsive idle mixture screw which could be used to regulate combustion in each cylinder at idle to give the lowest possible emissions. In time perhaps I will try this approach, but given that my carbs appear to have been balanced by the former (one-air-screw-closed) method I decided to try that first.
Adjustment:
I disconnected the throttle cable and set the motor to idle around 800 rpm using the idle speed adjustment screw and warmed the motor to temperature. I then stopped the motor, fitted the Carbtune spigots and connected the unit up. I then closed the air screws on all carbs and restarted the motor. The method calls for maximising the vacuum in each barrel using the idle mixture screws- I tried that but found little effect (see above).
I then opened the air screw on the stronger barrel in each carb to reduce vacuum to match that in the weaker barrel of each carb. The air bypass screws did have an effect and it was possible to set the pairs equal in each carb. I could then set the front and rear carbs to match using the carb synchronisation screw. I had synchronised the butterflies physically in the past and in fact this was very close to synchrony achieved by matching vacuum. Finally I reset the idle speed and rechecked the idle mixture screws- again with little effect.
At this point the carbs were all balanced by vacuum, but the motor had a misfire. This I assumed was due to incorrect mixture setting, so I adjusted the idle mixture screws and found one that clearly improved matters. In order to check this adjustment across all cylinders I used a pair of colortunes to check 2 at a time. These were installed in cylinders 1 and 2 or 3 and 4 and thus checked the output from both barrels of one carb at the same time. This also let me compare the colours in both cylinders.
I don't think the photos really show the colours but it was hard to see them anyway and involved a bit of guesswork- this step best done in darkness.
As above adjusting the idle mixture screws had little effect unless turned too far in which case and extreme lean or rich colour could be derived. I set the screws in the middle of this seemingly vast adjustment range listening for smooth running and checked that combustion colours on all cylinders were at least acceptable with vacuums still balanced.
I do not think the carbs are correctly adjusted - they are balanced but then you can balance them at any setting- it doesn't follow that they are balanced at the correct setting! On the credit side at least there is now a smooth idle and a balanced vacuum set. Any problems will become clearer I think if/when I can ever drive the car. One milestone now though was that since the carbs were at last set up (after a fashion) I was able to engage gear and actually move the car under its own power for I think the first time in some 15 years! I want to test the car before I make any more adjustments and in the long run I would like to try to balance using the all-air-screws open method.
One thing I will add is that all this taking out and in of spark plugs is a bit awkward. I invested in this Sealey plug starter tool which saved many a burned knuckle!
Checking combustion colour in cylinders 3 and 4 |
Flash picture of above |
As above adjusting the idle mixture screws had little effect unless turned too far in which case and extreme lean or rich colour could be derived. I set the screws in the middle of this seemingly vast adjustment range listening for smooth running and checked that combustion colours on all cylinders were at least acceptable with vacuums still balanced.
Vacs balanced across all 4 barrels |
One thing I will add is that all this taking out and in of spark plugs is a bit awkward. I invested in this Sealey plug starter tool which saved many a burned knuckle!
![]() |
Sealey spark plug installation tool- prevents cross threading and stops you burning your knuckles- it IS better than an old piece of vac hose! |